You have invested time and money in your ground support equipment (GSE) fleet, which includes aviation jacks, tows, GPUs, and HPUs to name a few. You depend on your GSE and expect minimal downtime and a long service life. However, a poorly implemented maintenance plan or no maintenance plan at all will eventually cripple your fleet and your business. Creating ground support equipment maintenance plans are worth the time and energy and are a critical investment.
Clearly Defined GSE Maintenance Planning
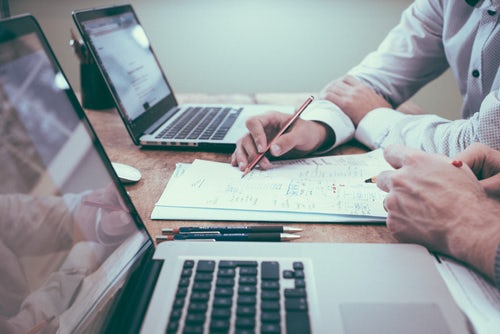
The benefits of a well defined maintenance plan is knowing what ground support equipment will be down for maintenance and when. A comprehensive GSE maintenance plan scheduled and followed takes the guesswork out of tasks, like when filters were last replaced on an HPU or when the oil will be changed on an aviation tug. Tasks such as fluid analysis and certification testing happen on schedule with minimal interruption to productivity.
Cost Savings
With ground support equipment maintenance plans in place, you will see an overall reduction in costs. Savings include costs for unexpected repairs, unscheduled downtime, as well as overall operational costs because equipment will run far more efficiently. From a financial viewpoint, an investment in a preventative maintenance plan for your GSE provides a positive ROI.
Optimal GSE Operation
When preventative maintenance is performed on your GSE, it enables the equipment to operate at optimum performance and efficiency. Issues that can negatively impact performance, such as hydraulic contamination or lack of lubrication, are minimized when a solid maintenance plan is put in place and followed.
Extended Useful Life of GSE
Properly maintained ground support equipment has a longer working life. Towbars, jacks, workstands, ground power units, and mules will work and maintain their value for a longer period of time. Maximizing the life cycle of GSE undeniably saves money.
Improved Reliability and Consistent Productivity of GSE
The operational reliability of your equipment will significantly increase once you are following a regular maintenance plan. Preventative maintenance addresses issues before they develop into problems and supports the early detection of parts or components that are on the path to failure. This increased reliability will also mean a consistently high level of productivity for the GSE fleet.
Creating Ground Support Equipment Maintenance Plans
Putting together robust, well-scheduled maintenance plans that prioritize the appropriate equipment is no minor task. It is critical that the right people be involved in developing the maintenance plan. Managers and employees working together with a GSE repair and maintenance provider are key to putting together a plan that is both thorough and feasible.
Any staff working regularly with ground support equipment should also be included in plan development, especially when it comes to scheduling. They should be kept in the loop and their feedback taken seriously. These are the workers who use the equipment regularly and are familiar with it and therefore can provide valuable information to the GSE maintenance provider performing the scheduled maintenance.
Once a diverse team is assembled and a GSE maintenance and repair company like FlyTek GSE has been hired, it’s time to set goals for the plan. Taking inventory of the equipment that will be included in the maintenance plan is an important step. A good plan will include information such as:
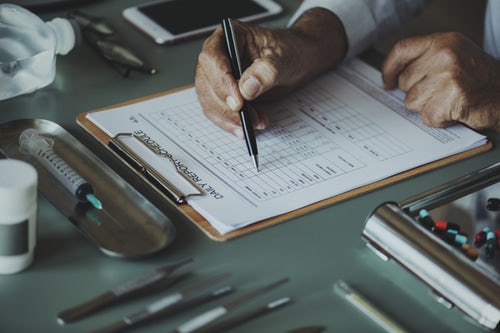
- Make and model of equipment
- Category
- Specifications
- Capabilities
- Department responsible for it
- Serial number or other type of identification
- Equipment location
For each piece of equipment, consider the status and appropriate goals based on age, condition and/or schedule. If it has been sidelined for months and is no longer in use, it probably doesn’t need to be included in the plan. On the other hand, if it is something you use every day, then it should be a top priority on your equipment list. Your GSE maintenance provider will help you with these decisions.
During this process, determine which ground support equipment maintenance plans are the highest priority. Then begin assigning tasks for the highest priority equipment first:
- What type of maintenance, testing, or certifications need to be performed?
- How often do they need to be performed?
- How is maintenance scheduled to minimize overall impact on productivity?
The final step, and often the trickiest, is scheduling the maintenance. This is where FlyTek GSE’s experience and knowledge is an enormous benefit.
Trust FlyTek GSE with Your Ground Support Equipment Maintenance Plans
The process of developing ground support equipment maintenance plans can be overwhelming and time-consuming, but FlyTek GSE can help. We will work with your team to develop an all-inclusive customized maintenance plan that supports the goals you have for your GSE assets.
Our technicians regularly work on brands such as Eagle Tugs, FoxCart, Hobart, JetMac, JetPorter, Lektro, TowFLEXX, Tronair, Unitron, and more. And we offer a wide variety of onsite maintenance and repair services, and that includes jacks (including aviation jack load testing and certification), tugs, towbars, engine slings, mules, GPUs, and any other type of ground service equipment in your fleet. We handle much of the maintenance, repair, and testing right onsite.
If you agree that it’s time to increase the reliability and lower the operational costs for your GSE fleet, contact us today. Our staff would be happy to schedule a free evaluation of your ground support equipment.